[ad_1]
At its compounding facility in Hong Kong, weplastic has the capacity to recycle 200 tonnes of polyethylene terephthalate (rPET) flakes per month, or around 10 to 12 40- feet containers, into rPET granules. These can then be upcycled into different products sold to final buyers.
The processed granules can also be sold through the firm’s existing sales channels in markets globally.
In Hong Kong, 2,331 tonnes of plastic waste were sent to landfill each day in 2021, accounting for the second-largest share of the city’s municipal solid waste at 20.5 per cent, according to the Environmental Protection Department.
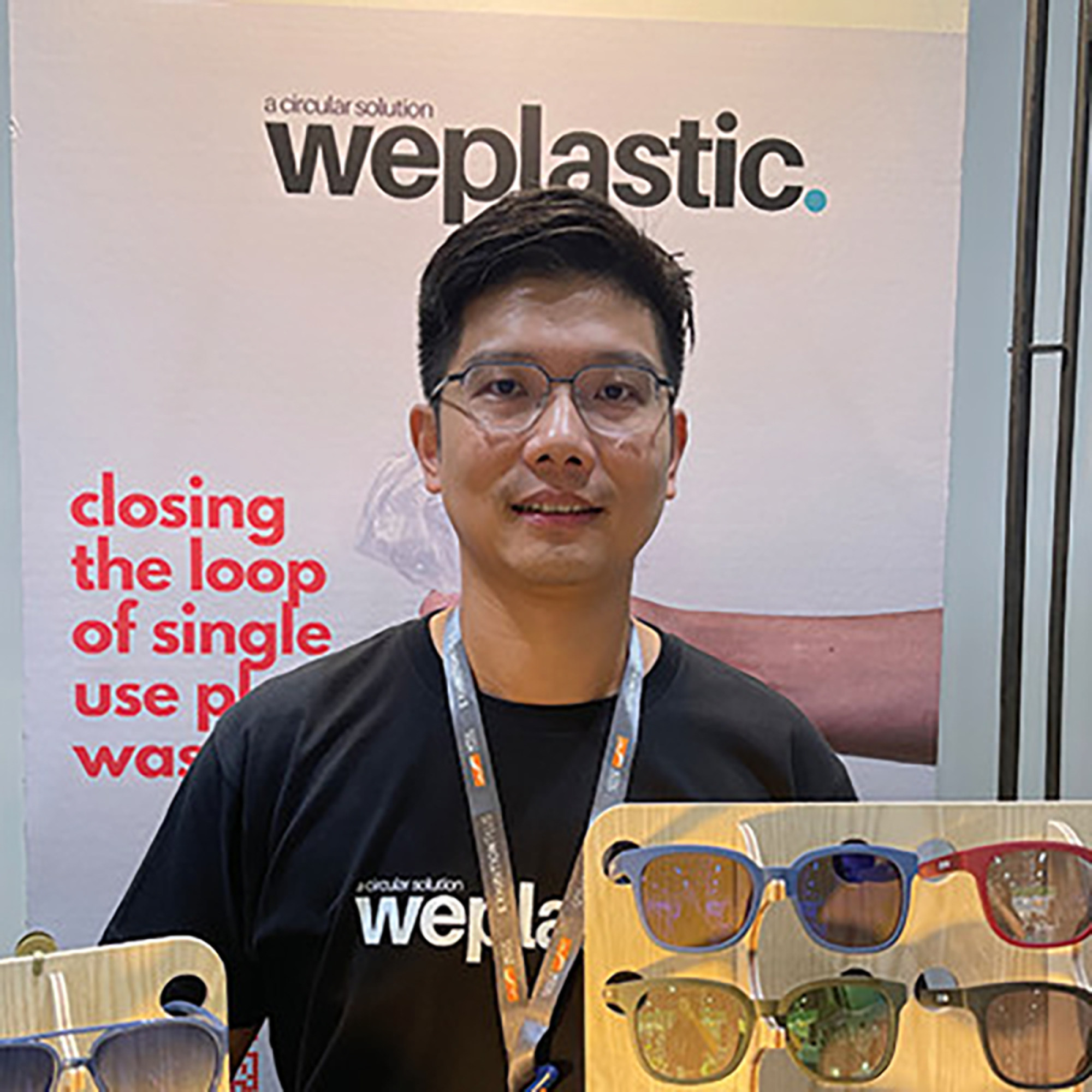
One of the challenges of scaling up the business has been the capital investment needed to maintain inventory.
“Capital investment [for] feedstock and processed granules is a major challenge, because we need to maintain at least three months of inventory for a scalable business,” Ma said.
“It is a profitable business for us, as our materials meet global standards due to technical know-how from Switzerland, but we need capital to run.”
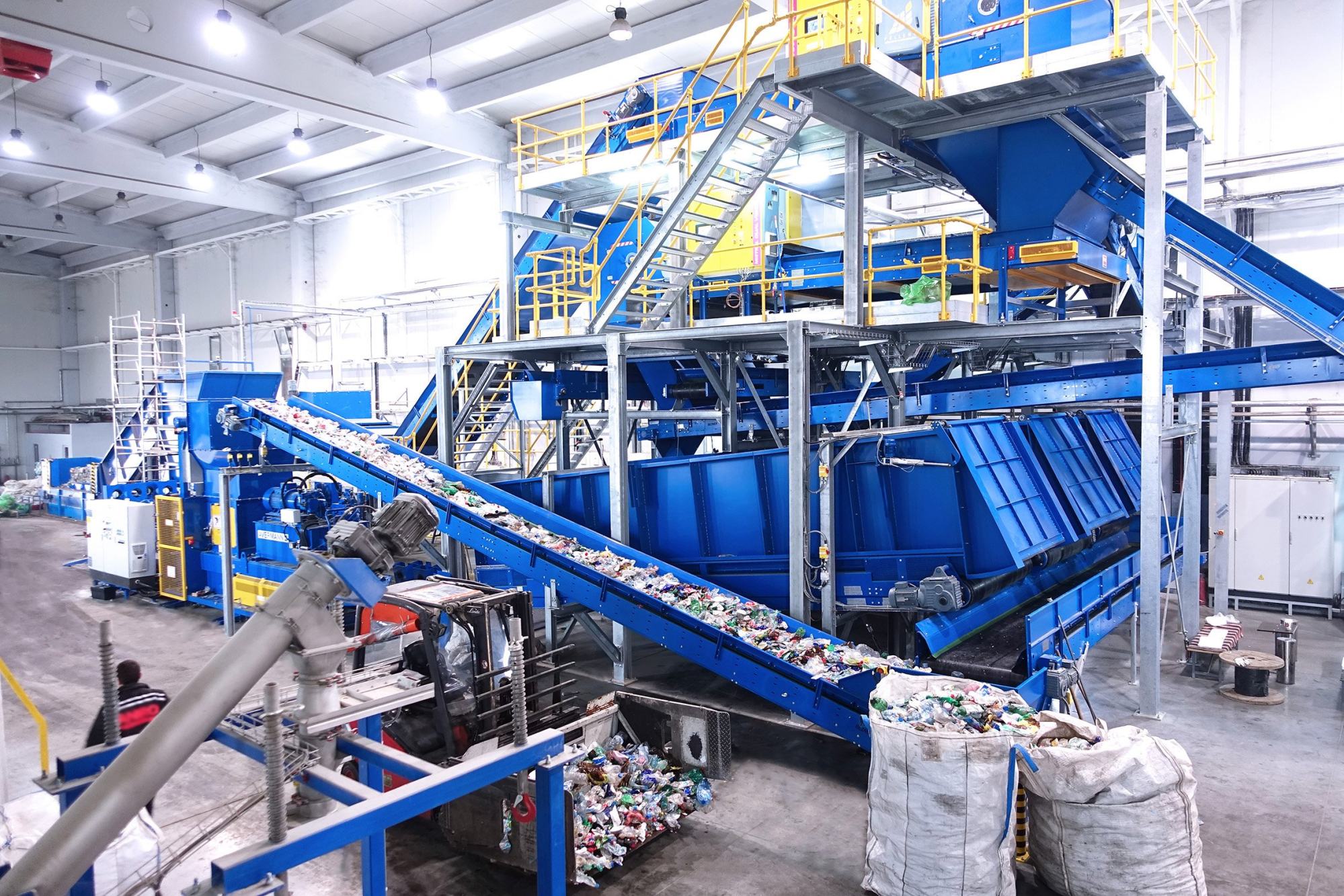
Through Ma’s business partner, Thomas Schori, founder of Switzerland-based #tide ocean material, the firm is able to access technical support and backup from the Swiss University of Applied Science.
Ma has known his partner for more than 15 years, having worked with him in the supply chain of the tanning industry.
“Recycling in Switzerland is a modern industry, which can be clean, elegant, modern and high-end,” Ma said.
Hong Kong marks Earth Day by recycling plastic waste, saving food for the poor
Hong Kong marks Earth Day by recycling plastic waste, saving food for the poor
Weplastic does not collect plastic waste itself, but the start-up is able to provide upcycling services to clients or companies for plastic collected by them. The plastic can be upcycled into sunglasses, tote bags, garments and other products.
It also blends coffee grinds collected from a local social enterprise into plastic materials, as a replacement for fossil-based dyes. The plastic retains coffee’s brown colour as well as its smell, and has been made into sunglasses with the help of weplastic’s supply-chain partners.
Elsewhere, Hong Kong-based FMC Manufacturing has been working with its partner Dynasty Vitality and the firm’s joint-venture company in Beijing to produce biodegradable resin from plant-based starch.
The resin can be made into compostable bags and other packaging materials, which have been used by a range of clients, including hotel brands in the Hong Kong market, as well as buyers in mainland China and overseas markets in Europe, the US and Australia.
FMC and its partner have the capacity to produce up to 5,000 tonnes of resin annually in their factory in the Beijing area, made from corn starch from northeastern China. The resin costs between 15,000 yuan (US$2,105) and 18,000 yuan per metric tonne, depending on its quality and characteristics.
“The major barriers preventing [these materials] from replacing plastics are the price, their shelf life, as well as the transparency or appearance of the material,” May Cheung, a partner at FMC, said in an interview.
Hong Kong’s new ‘green machine’ to take textile-recycling capacity to new level
Hong Kong’s new ‘green machine’ to take textile-recycling capacity to new level
FMC’s biodegradable resin costs at least twice as much as conventional plastic resin, according to Cheung. The products are best used to replace single-use disposable plastics such as plastic bags, she added.
Due to the molecular structure of the material, it begins gradually decomposing right after it is used, although at a really slow rate, which means the product cannot be used after being stored for a maximum of 24 months, Cheung said.
[ad_2]
Source link