[ad_1]
Amidst a waste problem worldwide that stinks from both a literal and climate change perspective, the founders of a Melbourne startup have decided it’s time for a nappy change.
That change is recycling.
Where others have tried and failed, DiaperRecycle has managed to pin down a business model that gathers used nappies through a subscription service with individuals and businesses, and at its Lilydale demonstration plant on the outskirts of Melbourne can process the diapers to produce a lightweight, absorbent cat litter, as well as plastic that is passed on to recyclers.
Perhaps the metaphor ‘pin down’ is misplaced, as it relates to the very fabric for nappies that would be a solution to this glaring problem if every parent or carer used them. But the fact is most don’t, and no amount of wishful thinking will alter the diversion of an estimated two billion nappies that go into landfill in Australia each year.
Willful action has potential though, and that’s what DiaperRecycle co-founders Clarke Kelland and Cynthia Barnicoat have been with this project, culminating in a technology and operation they aim to license to overseas partners within six to 12 months, and also launch into Sydney with a focus on aged care to recycle incontinence diapers.
Kelland tells Business News Australia the current plant has the capacity to process one thousand tonnes of nappies per year.
“But to make a really significant impact we want to be at 5,000-10,000 per plant, so that requires more capital beyond a couple more individuals,” says Kelland, who adds the whole venture was bootstrapped with around $2 million spent before a $335,000 crowdfund on Birchal late last year.
“A tonne of nappy waste generates about a tonne of CO2 in landfill. In our process we use energy and chemicals, and we would generate 200kg, so we’re saving 800kg for every tonne that’s out of landfill.
“The cat litter is actually quite unique. It’s half the weight of an equivalent recycled fibre cat litter; the dominant cat litters are either clays or newsprint pellets.”
This means that when that litter eventually goes to the tip, it generates less carbon dioxide and methane gas, which is the main problem influencing climate change when it comes to landfill.
“The benefits are high absorbency, lightweight which in this instance means about half the amount of carbon to look after your cat’s toileting needs, and also the logistics of carting it around because it’s half the weight. Aesthetically it’s white, just like the fibres in the nappy.”
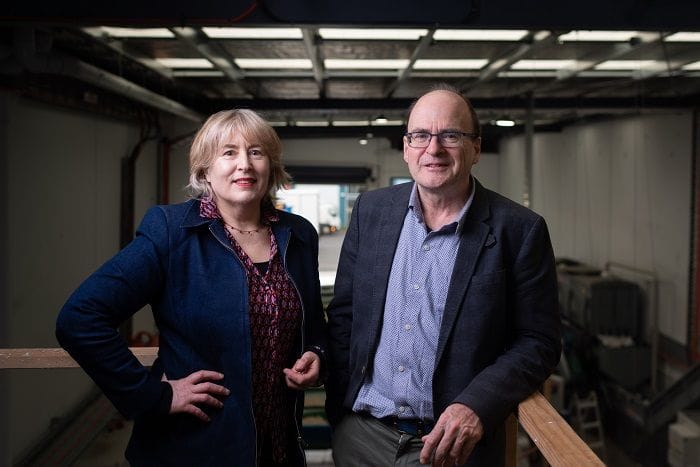
With a background as an engineering manager in the pulp and paper industry, the entrepreneur had prior knowledge of the raw materials that go into nappies. Firstly, there’s plastic with the inner and outer liners, then there’s cellulose fibre providing the soft cushioning embedded between plastic layers, followed by a super absorbent polymer that is added to the fibre.
He says 65 per cent of a standard nappy’s dry waste is non-plastic, which through DiaperRecycle’s process is separated through a series of shredders with counter-rotating discs, breaking the plastic into small strips where the fibre can be removed by using wash water.
“We’re able to wash a lot of that fibre away from the plastic, and a rotating drum that’s got holes in it – a trommel – slowly rotates. Going into that is a really dilute slurry of plastic strips and fibre,” the co-founder explains.
“The rotating barrels have 5mm holes that drain the slurry away from the plastic, so coming out one end of this barrel is the plastic strips, and going through the holes is the fibre slurry,” he says, adding the plastic can be sent to a recycler to be converted into basic products like bollards or planks.
“The fibre slurry then gets dewatered, and there’s multi-stage squeezing of the fiber. It’s really quite dirty water at that stage, and you progressively dilute, squeeze, dilute, squeeze.”
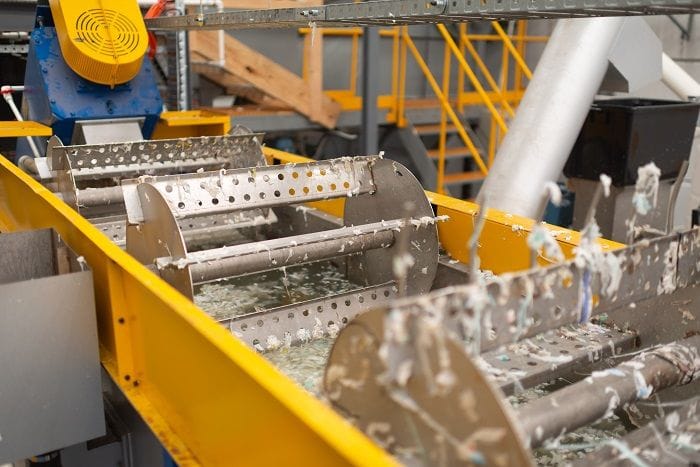
Each stage recovers water to use from the previous stage – a process known in the pulp industry as counter-current washing.
“So you minimise your water, but at the same time get a good wash. We use a sterilant that’s added as well to kill bugs,” he says.
“The fecal matter is broken down and then gets washed through screen plates, so 99 per cent of it is going out with the dirty water.
“The sterilant is in fairly high concentrations and holding times, because the EPA (Environmental Protection Agency) have told us what they want in terms of sterilisation efficiency.”
Kelland first got the idea to find a recycling solution for diapers 12 years ago when he was working at a company that was trying to do just that, but it ran out of money after a few years and folded.
“The idea from my time with that little startup, coupled with 20 years and the pulp and paper industry, I had some pretty good thoughts as to how to develop a technology that would work,” he says.
“I was sure I could work out the technology from my background, but for the economics I thought I’ve got to produce something that’s high grade and therefore most likely high value to provide the revenue to support the recycling process, which is quite an expensive process to run.
“Looking at others who attempted to recycle this waste, which have been numerous players over the last 20-30 years including most of the global corporates you can think of, I settled on the idea that it needed to produce a consumer price product, not a commodity price product.”
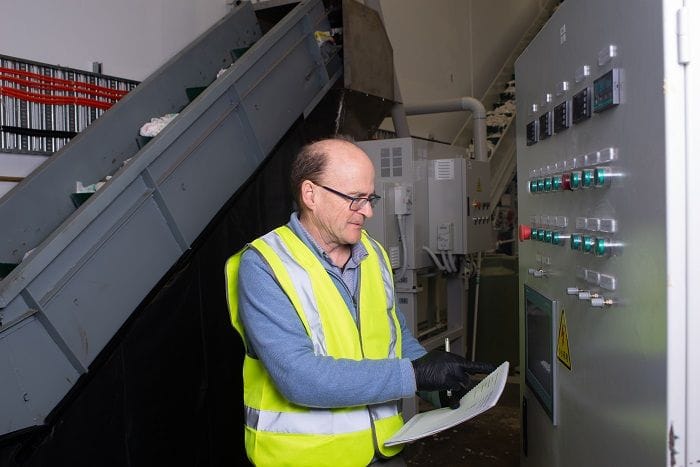
The first step in 2016 was to develop a prototype, so Kelland built a 50-square-metre shed in the Melbourne suburb of Abbotsford and bought a trommel from China to start tinkering with.
“I wasn’t prepared to take risks around jumping into the commercial space and taking a gamble on everything. So over a period of five years I basically tested equipment, and a lot of it was customised as well.
“We had a couple of dead ends, but that’s life when you try to do something that’s not happening – there’s no manual for it.”
The process progressively scaled up to the point where the technology and pilot plant were proven to work, so Kelland Environmental Technology Pty Ltd (trading as DiaperRecycle) was founded and registered as a company in 2019.
What followed was ongoing R&D while the technology, customer service side and product were refined, and after going through the Melbourne Accelerator Program in 2020, the following year the company started moving to the current facility in Lilydale, securing all the appropriate permits, and in April 2022 started operating from the site.
“It’s to demonstrate to others that the technology exists, it’s economically viable, it’s producing products that make sense, are in demand, and essentially it’s a circular economy. The idea is to scale beyond us,” Kelland says.
“We’re working on licensing agreements. In the UK there’s a waste collector who is actually a shareholder and he’s already got the logistics sorted. His customers are pushing him to get into a more environmentally friendly disposal option rather than burning it, which is quite a common thing to do in the UK.
“We’ve had interest from Denmark where there is a 2030 net zero carbon target. Now, they’ve worked out that you can’t get to 2030 net zero by ever burning – you actually have to recycle, so you’ve got government agencies scrambling to work out how to do it.”
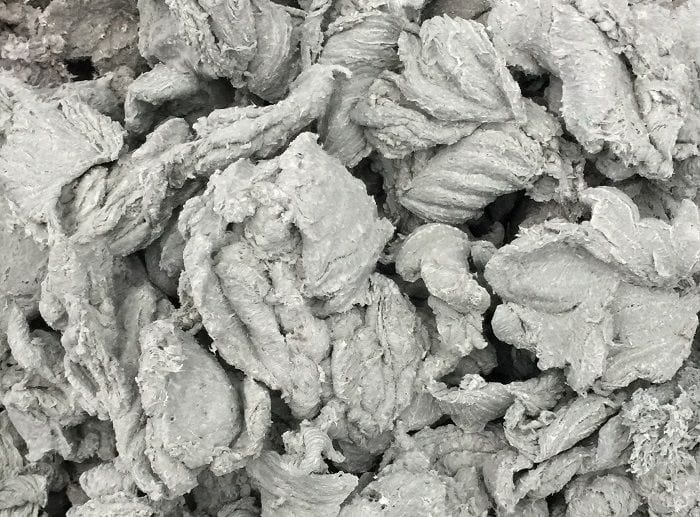
Interest in the technology has also come from Wales, South Africa, Germany, Ukraine, India and the US, where in Kansas City there is a non-profit that distributes nappies and wants to close the loop.
In Melbourne the biggest customers for the end product are currently catteries, although there are a few households that buy the cat litter. Regarding the procurement of the dirty nappies, he says the system with subscribers works through a fortnightly pick-up.
“We’ve got vans, and we go and pick up the nappy waste. Households have to be in clusters, otherwise it’s uneconomic – you need at least half a dozen people in a reasonable radius because of the cost, and we’re mindful of the carbon footprint of that and we’ve got to get that right,” he says.
“We’ve got a few childcare centres on board. There seems to be more growth with them, it’s really quite interesting and the logistics are easier. For a pick-up at a childcare one bin is 300 nappies; one bin at a household is 60.
“Another big one is aged care, and that’s really where the big scale. Our ambitions are to go into Sydney which is a huge market in terms of incontinence waste, the landfill fees are very high. So beyond Lilydale, we see Sydney is the next port of call, and then it’ll be Brisbane.”
He says subscription rates are currently fairly flat for individual households, but that’s mainly because DiaperRecycle hasn’t pushed for numbers very hard yet while the team made sure the operation worked efficiently and effectively.
“Now we’re at a point where we can process the volume,” he says.
“People can come on board and invest, and then we can scale it beyond and then really hit the emissions, because that’s what’s really driving it apart from doing something interesting. This whole climate change exercise, it’s horrendous.”
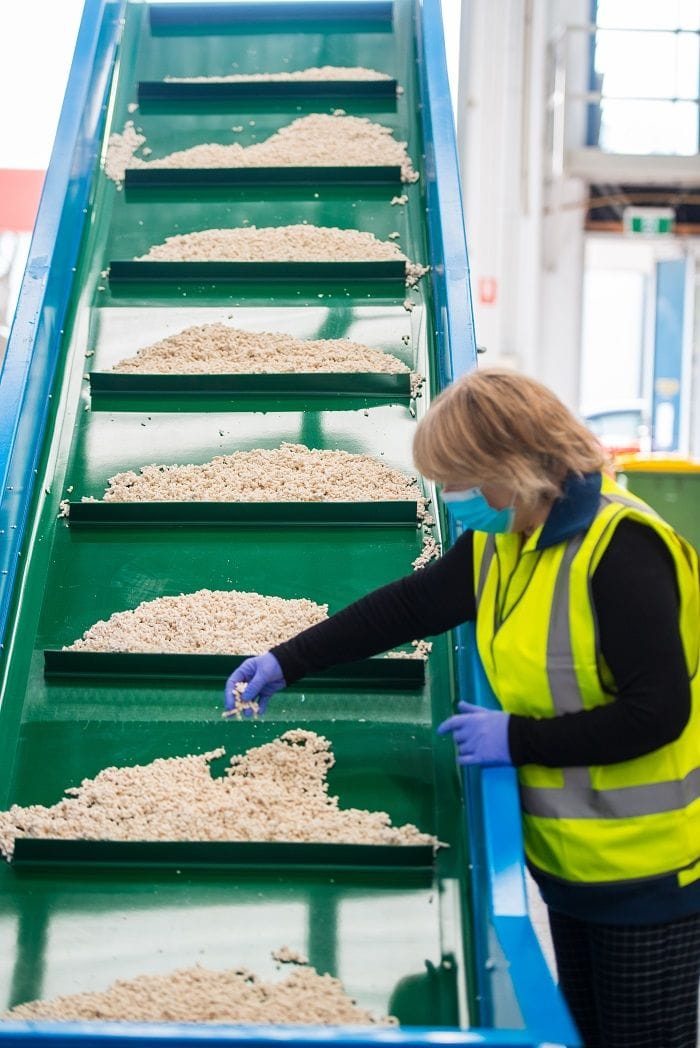
Get our daily business news
Sign up to our free email news updates.
Help us deliver quality journalism to you.
As a free and independent news site providing daily updates
during a period of unprecedented challenges for businesses everywhere
we call on your support
[ad_2]
Source link